Alumínium és alumínium-öntvények felületkezelése és korrózióvédelme
Alapanyag:
Az alumínium az egyik legsokrétűbben alkalmazott, ma már az ipar és a mindennapok számára nélkülözhetetlen, gazdaságosan előállítható jó elektromos vezető tulajdonságú fém. Kis sűrűsége miatt könnyű, rendkívül jól alakítható, megmunkálható, önthető, vagy kovácsolható, csekély mechanikai ellenállású anyag. Különböző ötvöző anyagok hozzáadásával (legjellemzőbben: Magnézium (Mg) Szilícium (Si) réz (Cu)) azonban sokféle módon tudjuk befolyásolni a mechanikai, kémiai, esztétikai és egyéb tulajdonságait. Így az iparban és a mindennapi életünkben szinte mindenhol jelen van, a háztartásoktól kezdve (alufólia, mindennapi használati tárgyak, díszítő elemek, stb.) az autóiparon át a repülés és űrtechnikáig alkalmazzák.
Az alumínium és az alumínium-ötvözetei úgynevezett amfoter jellegű igen reakcióképes fémek, mind savakkal, mind lúgokkal könnyen reakcióba lépnek, így kevéssé ellenállóak a savas vagy lúgos környezeti hatásokkal szemben, mint például a CO2-tartalmú nedves levegő. A tiszta alumínium fém felülete azonnal reagál a levegőben lévő oxigénnel és a felületén egy vékony, szürkés-fehéres alumínium oxid (Al2O3) réteg képződik természetes úton, ami valamivel ellenállóbbá teszi a további oxidációval, korrózióval szemben. Idővel ez a réteg természetes úton tovább vastagodhat, ami így megvédi és egyre ellenállóbbá teszi az alapfémet a környezetével szemben, azonban ez a természetes folyamat lassú.
A mai modern felületkezelési, felületvédelmi vagy korrózióvédő eljárások ezt a fenti lassú természetes folyamatot gyorsítják fel mesterséges úton, ellenőrzött körülmények között segítik elő az alumínium-alapfém felületének védelmét a mesterségesen létrehozott alumínium-oxid réteg kialakításával.
A továbbiakban, a teljesség igénye nélkül szeretnénk egy rövid áttekintést nyújtani az alumínium és alumínium-öntvények esetében leggyakrabban alkalmazott felületkezelő, felület- és korrózióvédelmi technológiákról és azok leggyakoribb alkalmazásairól.
Emellett szeretnénk segítséget nyújtani Vevőink számára a megfelelő felületkezelési technológia kiválasztásában és annak megfelelő alkalmazásában, kivitelezésében, elkerülve a legtöbbször előforduló buktatókat, a tervező asztaltól a megvalósításig.
A legtöbbet alkalmazott Felületkezelési technológiák, felület- és korrózióvédő hatásuk növekvő sorrendjében:
- Pácolás (Fehérítés)
- Kromát konverzió (Kromátozás)
- Alumínium anódos oxidációja (ELOXÁLÁS)
Pácolás (Fehérítés)
Az alumíniumpácolás (Fehérítés) alapvetően egy vegyszeres felületkezelési, felülettisztítási eljárás, ami a technológiai folyamat természetes következményeként minimális korrózióvédelmi hatással is rendelkezik.
A Pácolási (Fehérítés) eljárás célja és leggyakoribb alkalmazása az alumínium termékek, az öntött illetve a kovácsolt alumínium munkadarabok felületének megtisztítása az öntési, kovácsolási, edzési folyamat vagy a megmunkálás közben ráégett, rárakódott szennyeződések eltávolítása.
Pácolás (Fehérítés) Folyamata:
- Zsírtalanítás: a pácolási folyamat első lépése a meleg zsírtalanítás, ami eltávolítja az alumínium munkadarab felületéről a gyártási folyamatban rárakódott zsírokat olajokat, és nedvesíthetővé teszi a felületet a további vegyszeres kezelés számára.
- Lúgos maratás: a következő lépés a lúgos felületkezelés (maratás), ekkor az alumínium felületéről lúgos fürdőbe (legtöbb esetben híg NaOH) mártva nagyon kis mennyiségű alumínium réteget távolítunk el és aktiváljuk a felületet.
- Öblítés: mosással, öblítéssel eltávolítjuk a maratás közben keletkező lemosható szennyeződéseket, oxidokat, hidroxidokat.
- Savas maratás, oxidmentesítés: Öblítés után az alumínium munkadarabokat savas (általában híg salétromsav (HNO3), híg kénsav (H2 SO4)) fürdőbe mártjuk, ahol teljesen eltávolítjuk a felületről a jól tapadó lúgos maratás közben keletkező maradék oxidokat, hidroxidokat is, így fémtiszta alumínium felületet nyerünk.
- Melegvizes öblítés: A pácolás (Fehérítés) utolsó, de annál fontosabb lépése a melegvizes öblítés, illetve az ezt követő szárítás és sűrített-levegős lefúvatás, így a kész esztétikus munkadarab felülete foltmentes világos alumíniumszürke, homogén megjelenésű lesz.
- A pácolandó alumínium munkadarabok szennyezettségétől függően a fenti folyamatot akár többször is szükséges lehet elvégezni, amíg a végeredmény a várt esztétikus megjelenést nem éri el.
- A pácolási folyamat végeredményeként kapott fémtiszta felületen az öblítés és a levegővel való érintkezés hatására új, vékony alumínium-oxid réteg alakul ki, ami minimálisan megvédi a felületet további környezeti hatásokkal szemben.
Azonban lényeges megemlíteni, hogy a pácolási folyamat indokolatlanul hosszú vagy többszöri alkalmazása tönkre teheti a munkadarab tűréssel rendelkező geometriai méreteit, így az elvárásokról mindig egyeztetni kell a Megrendelővel.
Cégünknél a pácolási folyamatban teljesen automatizált gépsor biztosítja a technológia paraméterek és a késztermék minőségének állandóságát.
Pácolás (Fehérítés) előnyei:
- Szennyeződésektől mentes, egységesen homogén, esztétikus, tiszta megjelenés
- Emellett minőségbiztosítási szempontból fontos, hogy a pácolt felületen láthatóvá válnak az öntés, kovácsolás vagy megmunkálás közben esetlegesen előforduló kisebb nagyobb hibák, így kiszűrhetőek a nem megfelelő darabok.
- Minimálisan védett felület a környezeti korrózióval szemben
Kromát konverzió (Kromátozás)
Fém felületek korrózió védelmében az egyik leggyakrabban alkalmazott Fflületvédelmi eljárás az úgynevezett kromát koverziós kezelés (Chromate Conversion Coating (CCC)), vagy egyszerűbben kromátozási eljárás. A kromátozás elsősorban az alumínium, alumíniumötvözetek és horganyzott vas és acél munkadarabok passziválására szolgál, de alkalmazható önmagában vas és acél, cink, kadmium, réz, ezüst, magnézium és ónötvözetek esetében is.
A kromátozási eljárás során, az oldat hatértékű krómvegyületeinek Cr(VI) (vagy Cr(III) esetleg egyéb nemes fémvegyületeinek hatására - melyről nevét is kapta - a védendő kevésbé nemes fém felületen konverziós folyamatok mennek végbe. A krómoxid vegyületek beépülnek a védendő fém, esetünkben alumínium felületébe, illetve a felület mikropórusaiba, és egységes, egybefüggő néhány molekula, pár tized mikron (0,2-0,8µm) vastagságú zárt passzív réteget hoznak létre, ezt nevezzük kromát konverziós rétegnek.
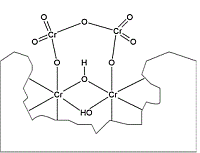
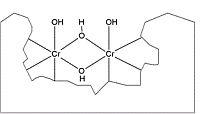
Cr(VI)- Cr(III)-
A legtöbb jármű, autóelektronikai és műholdalkatrész alumíniumból készül, melyeket általában kromát konverziós eljárással (Kromátozással) felület kezelnek.
A hat, illetve három vegyértékű kromátozással (Cr6+, és Cr3+ vegyületekkel) kezelt alumínium alkatrészeknek igen jó a korrózióval szembeni ellenállásuk, és megtartják kiváló felületi elektromos vezetőképességüket, emellett jó hővezetést és kiváló adhéziót biztosítanak a későbbi bevonatokhoz (festés, porfestés, ragasztás, hegesztés, stb.), azonban mechanikailag ellenállásuk gyengébb, sérülékenyebbek, mint például az eloxált alumínium felületek.
- Hatvegyértékű Cr(VI), „sárga” kromátozás
A hatértékű kromátozási eljárással felületkezelt alkatrészek könnyen felismerhetők (irizáló-) sárga színükről, ami miatt az eljárást "sárga kromátozásnak" is nevezik.
Emellett érdemes megjegyezni, hogy a Cr6+ vegyületekkel kezelt kromátozott felületek úgynevezett „öngyógyító” mechanizmussal is rendelkeznek. Amennyiben a kromátozással védett felület mechanikai sérülést szenved, a felületen lévő Cr(VI) oxidok „öngyógyító” módon újra passziválják a környezetükben levő nyers fémfelületet.
A jelenleg hatályos törvényi szabályozás ugyan még nem tiltja a hatvegyérték Cr(VI)tartalmú vegyületek használatát, azonban az Európai REACH, ROHS, ELV szabályozás ajánlásokat tesz a Cr(VI) tartalmú vegyületek használatának fokozatos elkerülésére, illetve használatuk kiváltására, azok egészségkárosító és rákkeltő hatása miatt. Ennek értelmében egyre kevésbé alakalmaz(ható)ott eljárássá válik a „sárga” Cr(VI) kromátozás.
A sárga kromátozás kiváltására ma már szerencsére több megfelelő Cr(VI) mentes megoldás is kifejlesztésre került, melyek műszaki tartalom tekintetében teljesen egyenrangú megoldást nyújtanak.
A legtöbbször alkalmazott alternatív megoldást a háromvegyérték Cr(III) tartalmú vegyszerek használata jelenti a kromát konverziós réteg kialakításához. Azonban napjainkban már léteznek krómmentes vegyszerrendszerek is, ahol a nemes Cr vegyület szerepét egyéb jó korrózióvédő tulajdonságokkal rendelkező fém helyettesíti, mint például a Stroncium (Sr) vagy Titánium (Ti).
- Háromvegyértékű Cr(III) kromátozás
A háromvegyértékű Cr(III) kromát konverziós réteg kialakítása gépészeti technológiai szempontból teljesen hasonlóan működik, mint a korábbi hat vegyértékű rétegeké, azonban a vegyszerek költsége magasabb és könnyebben kimerülnek, így pótolni kell azt, ami további költségtényezőt jelenthet.
Emellett a megfelelő háromértékű kromátréteget nehezebb kialakítani. Ugyanis az eljárás közbeni környezeti paramétereket (koncentráció, az oldat PH értéke) egy nagyon keskeny tartományban kell tartani a hatértékű eljáráséhoz képest.
A Cr(III) kromátozott felület előnyös tulajdonságai, mint
- igen jó a korrózióval szembeni ellenállásuk, és
- megtartják kiváló felületi elektromos vezetőképességüket,
- emellett jó hővezetést és kiváló adhéziót biztosítanak a későbbi bevonatokhoz (festés, porfestés, ragasztás, hegesztés, stb.).
- azonban mechanikailag ellenállásuk gyengébb, sérülékenyebbek.
Az egyetlen lényegi különbség, hogy a háromértékű Kromátozás a munkadarab felületén egy áttetsző, irizáló passzív réteget hoz létre.
Kromát konverzió réteg (Kromátozás) létrehozásának folyamata:
- Zsírtalanítás: a kromátozási folyamat első lépése a meleg zsírtalanítás, ami eltávolítja az alumínium munkadarab felületéről a gyártási folyamatban rárakódott zsírokat, olajokat és nedvesíthetővé teszi a felületet a további vegyszere kezelés számára.
- (Opcionális) Lúgos maratás: (Opcionális lépés, amennyiben az alkatrész szennyezettsége azt megköveteli) a következő lépés a lúgos felületkezelés (maratás), ekkor az alumínium felületéről lúgos fürdőbe (legtöbb esetben híg NaOH) mártva nagyon kis mennyiségű alumínium réteget távolítunk el és aktiváljuk a felületet.
- Öblítés: mosással, öblítéssel eltávolítjuk a maratás közben keletkező lemosható szennyeződéseket oxidokat, hidroxidokat.
- Peroxidos (H2O2) savas maratás, oxidmentesítés: Öblítés után az alumínium munkadarabokat savas (általában peroxidos híg kénsav (H2 SO4)) fürdőbe mártjuk, ahol teljesen eltávolítjuk a felületről a jól tapadó maradék oxidokat, hidroxidokat is, így fémtiszta alumínium felületet nyerünk.
- Kromát konverziós réteg kialakítása (Kromátozás): A fémtiszta, szennyeződésektől mentes felületű alkatrészeket krómtartalmú 25-40 °C hőmérsékletű, pontosan beállított pH-jú fürdőbe merítjük. 30 – 120 másodpercig tartó kezelési idő alatt kialakítjuk jól tapadó kromát konverziós réteget az alkatrész felületén.
- Melegvizes öblítés: Kromátozási folyamat utolsó, de annál fontosabb lépése a melegvizes öblítés, illetve az ezt követő szárítás és sűrített levegős lefúvatás, így a kész esztétikus munkadarab felülete folt mentes világos alumíniumszürke, homogén megjelenésű lesz.
ELOXÁLÁS
Alumínium, alumínium-öntvények vagy alumínium ötvözetek környezeti hatásokkal szembeni ellenállóvá tételére általánosan alkalmazott felületvédelmi eljárását anódizálásnak (anódos oxidációnak), vagy a mindennapi életben elterjedten eloxálásnak nevezzük.
Az eloxálás során az alumíniumot híg savban (kénsav, foszforsav, oxálsav, krómsav stb.) anódként kapcsolják (+ pólus), ekkor vízbontás játszódik le, az anódon oxigén fejlődik, a katódon hidrogén. A fejlődő oxigén azonnal reagál az alumíniummal és porózus oxidréteget hoz létre a felületen.
Az eloxálásnál a réteg keménysége az eljárás paramétereitől függ (alkalmazott feszültség, hőmérséklet, az alkalmazott sav-koncentráció stb..).
Általánosan eloxálásnak (elektrolitikus oxidáció alumínium felületen) nevezzük azt az eljárást, amikor 180-200 g/l-koncentrációjú híg kénsavban 18-20 °C-on 15-20 V feszültséggel,
1,5-2,0 A/dm² áramsűrűséggel anódizálunk.
Az európai szabványok az Eloxálásnál 5-10-15-20-25 µm szabványos rétegvastagságot írnak elő. Az ennél vastagabb 30-35 µm rétegvastagság az úgynevezett kemény eloxálással (vagy hard-elox) eljárással érhető el. A kemény eloxáláshoz azonban gyengébb vezetőképességű elektrolitra és lényegesen alacsonyabb fürdőhőmérsékletre van szükség, azonban az így végzett eloxálás hatására a kialakuló Al2O3 (Korund) réteg tömörebbé válik.
Mindkét lényegében hasonló eloxálási eljárással porózus, felületi oxid-réteget hozunk létre.
Az így mesterségesen létrehozott porózus oxidréteg kiváló korrózió és kopásálló rétegként védi az Alumínium alapfémet, emellett egységes homogén megjelenést biztosít a munkadarab számára.
Az eloxálás során a pórusok lehetőséget adnak a felület színezésére:
- Elektrolitikus színezés: Amennyiben fémeket választunk le elektrolitikusan a pórusokba, akkor elektrolitikus színezésről beszélünk. Például ón-szulfáttal a pezsgőszíntől a feketéig lehet színeket előállítani.
- Abszorbciós színezés: Használhatunk ezenkívül szerves színezékeket, itt egyszerűen belemártjuk az eloxált anyagot a színezékbe. A szerves színezékkel előállított színek a napfény hatására egy idő után kifakulhatnak, kevésbé UV-állók, mint felületre leválasztott fémvegyületek színei.
Az eloxált felületeknél a korrózió- és kopásállóság szempontjából a legfontosabb lépés a folyamat végén a porózus oxidréteg pórusainak megfelelő tömítése (sealing). A felületi tömítettség határozza meg a korrózióállóságot mind natúr, mind színezett termék esetén. Színezett termék esetén nemcsak a korrózióállóságot, hanem a színtartósságot is erősen befolyásolja.
A tömítés történhet
- forróvízben (95-98 °C) (HOT-sealing) vagy
A forróvizes tömítés lassabb, és energia igényesebb megoldás, azonban nem tartalmaz idegen fém-sókat a pórusok zárására.
- Nikkel-fluorid oldatban (COLD-sealing).
A hideg-tömítési eljárás gyorsabb, energiaköltség hatékonyabb és korrózió állóbb eljárás, azonban hozzáadott nemesebb fémionokat tartalmaz.
- Kombinált tömítés kromát oldatban (Kromát-sealing).
Speciális igény esetén hideg kromát-tömítési eljárással tovább növelhető az Eloxált felület egyébként is kiváló korrózió állósága, illetve korlátozott mértékben az egyébként elektromosan szigetelő eloxált felületi réteg vezetőképessége is javítható.
Ez az eljárás, azonban nem egyenértékű a kromát konverziós réteg egységesen egybefüggő védőrétegének elektromos vezetőképességével, mivel a kromátozó vegyszer itt bediffundál a nyitott pórusokba, így biztosítva a felület tömítettségét. Azonban a hozzáadott korrózió-védő hatása jelentős.
Az eloxálás során a korrózióállóság tovább növelhető átlátszó lakkozás/póruszárás alkalmazásával, de ez költségesebb az egyszerű tömítésnél, és a legtöbb esetben nem is képvisel jelentős többlet hozzáadott értéket a felhasználás szempontjából.
Eloxálás technológiája, az alumínium anódos oxidációja
Az anódos oxidáció
Habár alumínium amfoter jellegű fém, így savakkal és lúgokkal is könnyen reakcióba lép, mégis az alumínium kiváló korrózióállósága közismert. Ezt a tulajdonságát a természetes módon a felületén kialakuló tömör oxid rétegnek köszönheti, ami megvédi a további korróziótól az alapfémet (Al2O3, vagy közismerten korund, ami természetben előforduló második legkeményebb anyag a gyémánt után).
Az anódos oxidáció vagy más néven eloxálás ezt a természetben lezajló folyamatot hivatott elvégezni mesterséges körülmények között. Az alumíniumot híg savban (foszforsav, oxálsav, kénsav, krómsav stb.) anódként kapcsoljuk (pozitív pólus). Az anódon oxigén fejlődik, a katódon hidrogén. A fejlődő oxigén azonnal reagál az alumíniummal és porózus oxidréteget hoz létre. Végfelhasználástól függően változtatható az oxid-réteg vastagsága.
Natúr, színtelen eloxálás: kopás- és korrózióálló, illetve díszítő rétegként általában 5-15 µm rétegvastagságban, illetve nagyobb kopás és korrózió állóságú ipari alkalmazások esetében 10-25 µm rétegvastagságot alkalmazzuk.
Színezéskor a képződött oxidréteg csőszerű pórusaiba juttatunk adszorpciós (kémiai), vagy elektrolitikus (fémoxid leválasztás) úton szín pigmenteket.
A folyamat végén a pórusokat az úgynevezett pórustömítéssel lezárjuk, így tartósan korrózióálló, nem fakuló felületet kapunk.
A tömítés történhet
- forróvízben (95-98 °C) (HOT-sealing) vagy
- Nikkel-fluorid oldatban (COLD-sealing).
- kombinált tömítés kromát oldatban (Kromát-sealing).
A technológia
A tökéletes minőségű oxidréteg eléréséhez elengedhetetlen, hogy a munkadarab felülete tiszta, homogén, zsírtól és olajtól, és oxidoktól-mentes, kiválóan nedvesíthető legyen.
Ennek eléréséhez a technológiai sor mindig zsírtalanítással kezdődik.
A technológiai folyamatok között többszöri öblítés szükséges.
A lúgos maratás/szatinálás (szatén) opcionális lépés lehet, a zsírtalanítást követően homogén matt felület alakítható ki vele.
ELOXÁLÁS folyamatábra:
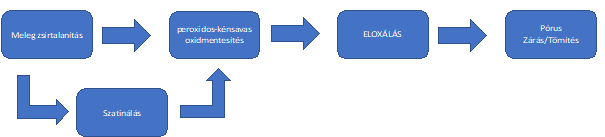
Az eloxálási művelet után pórustömítés következik. A pórustömítés forró vízben vagy nikkel-só tartalmú oldatban történik leggyakrabban. Az eloxált felület megjelenése színe erősen függ az alumínium ötvözőinek minőségétől és mennyiségétől. Az ötvözők mennyiségének növekedése rontja az alumínium-ötvözetek ELOXÁLHATÓSÁGÁT.
A következő táblázat mutatja az ötvöző anyagok hatását az ötvözetek ELOXÁLhatóságára:
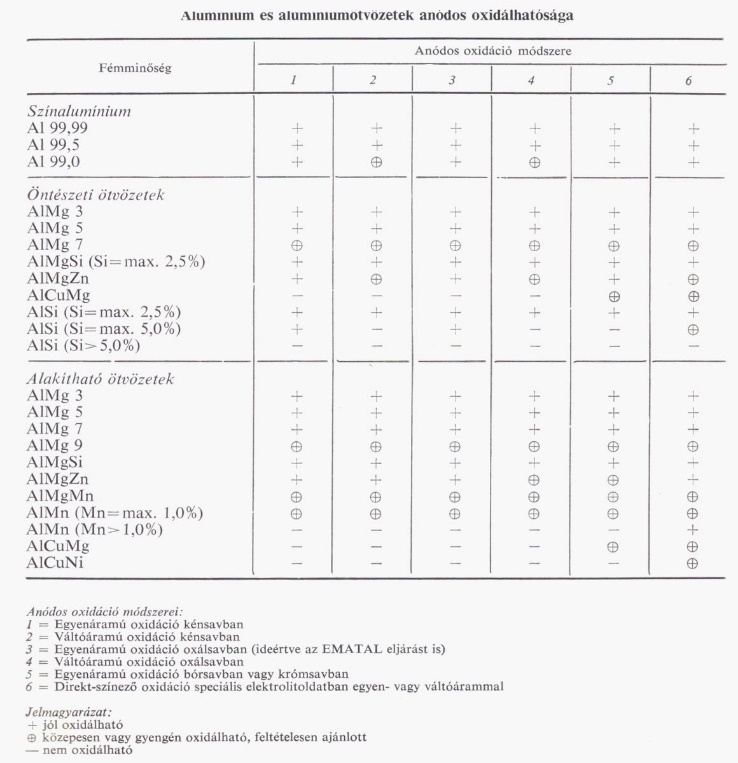
Az alumínium-oxid (Al2O3 ) vagy korund a természetben előforduló második legkeményebb ásvány. Különleges igénybevételű alkatrészek esetén ahol a súrlódásból adódó kopás veszélye áll fenn, jó megoldást nyújt az ún. kemény eloxált felület.
Kemény eloxálásnál a fürdő vezetőképességét csökkenteni és erősen hűteni kell (0-5 °C). Alacsony hőmérsékleten az oxid visszaoldódás folyamata lelassul, viszont a képződő oxid réteg pedig tömör, porózusmentesebb lesz. A jellemző rétegvastagság 30-80 µm.
A felület megjelenése szürke, sötét szürke, esetleg fekete árnyalatú lesz az ötvözet minőségétől függően.
Az Unicorn Kft.-nél elérhető Eloxálások
- Natúr színtelen ELOX: 5-15 µm rétegvastagságban 20%-os kénsavban
- Natúr színtelen/szürke ELOX 10-25 µm rétegvastagságban 20%-os kénsavban
- Kombinált, kromátozott ELOX 5-20 µm rétegvastagságban 20%-os kénsavban
Az ELOXÁLÓ gépsor technológiai kialakítása lineáris. A technológiai lépéssor a felrakó/leszedő pozícióhoz közelebb eső zsírtalanító fürdőben indul. Zsírtalanítás/illetve, ha szükséges Szatinálás után (2x) öblítés következik, majd a következő lépés a peroxidos oxidmentesítő kénsavas pácolás. Ezt követi maga a natúr normál ELOXÁLÁS lépése. Eloxálás után ismét kaszkád öblítés (2x), majd szükség esetén kromátozás a követő lépés. Az oxidálás végső technológiai lépése a pórustömítés, ami történhet Nikkel-só oldatban vagy 96-98°C-os lágy vízzel.
A sor elmélet kapacitása natúr eloxálás esetén kb.: 6m2/ óra eloxált felületre vonatkozóan. A gépsor kádjain perem elszívás van kiépítve 2 x 12000 m3/óra kapacitással.
Az üzemünkben működő szennyvízkezelő berendezés végzi az üzemben képződött összes szennyezett öblítővizek, illetve az egyéb technológiai víz tisztítását. A folyamat lényege az, hogy a vízben lévő oldott fémeket, alumíniumot eltávolítsuk, a pH-értéket a kibocsátható 6-10 értékre állítsuk be.
A rendszer automatikusan működik. Emberi felügyeletet ugyan igényel, hogy a szükséges vegyi anyagokat folyamatosan pótolni tudjuk a beoldó tartályokba. A fém- és az alumínium sókat a reaktorban mésztejes pH-állítással pH=9,5 értéken kicsapjuk a vízből fém -karbonát, -hidroxid csapadék formájában (Al(OH)3). A csapadék az alkalmazott flokuláló szer hatására nagy méretű, jól ülepedő formában kerül az ülepítő tartályba. Innen a tiszta víz elfolyik, kavicsszűrőn keresztül kerül a folyamatos önellenőrzés és időszakos hatósági ellenőrzés mellett a közcsatornába.
A kiülepedett csapadékot szűrőprésre nyomjuk, az ott keletkező iszapot pedig big-bag zsákba ürítjük, majd elszállíttatjuk ártalmatlanításra.